The hybrid heat pump constitutes one of the core elements of the HyCool solution for solar cooling in industry and, therefore, its optimal design is crucial to achieving high performance of the overall system. Since the very beginning of the project, the Fahrenheit team has been working on a prototype of the hybrid heat pump with the goal of obtaining highest efficiency while keeping the machine simple and reliable. In the early spring of 2019, the first prototype HyCool XHHP01 was ready for testing. The results of the tests performed by CNR have shown a very good performance of the prototype and have indicated a few areas, which still needed improvement. Currently, the Fahrenheit team is making use of the time left before the installation of the pilot sites to optimize the functionalities of the hybrid heat pump. Three members of the team explain to us the general concept of the hybrid heat pump, how they want to optimize the prototype, and what challenges are still ahead of them.
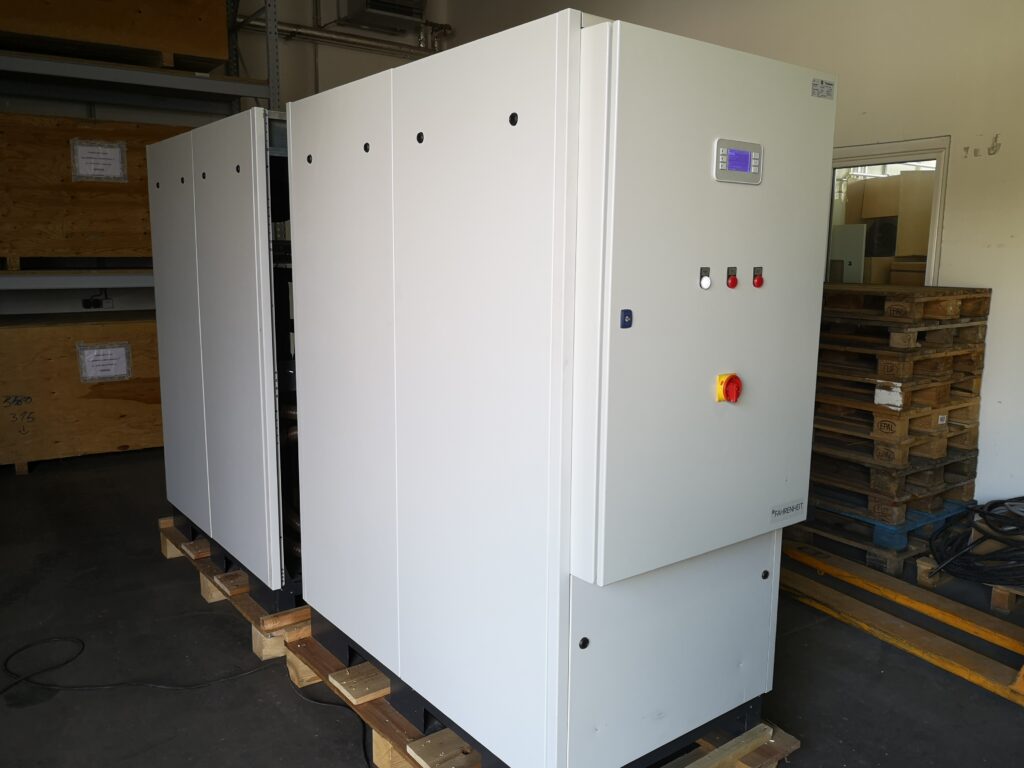
The hybrid heat pump constitutes one of the core elements of the HyCool solution for solar cooling in industry and, therefore, its optimal design is crucial to achieving high performance of the overall system.
Eliza Nowak, Project Engineer at Fahrenheit GmbH, on the general concept of the hybrid heat pump
The term “hybrid” refers to a combination of two or more interconnected and co-operating heat pumps based on different principles of operation. In our case, the developed prototype consists of an adsorption and a compression heat pump connected in such a way that the evaporator of the adsorption unit cools down the condenser of the compression one. This lowers the condensation temperature below the one resulting from the outdoor conditions. Lower condensation temperature means higher EER (Energy Efficiency Ratio – ratio of the delivered cooling capacity to the consumed electrical power) of the compression chiller. Of course, to make this layout feasible, the savings of the electrical power consumption of the compressor due to higher EER should be higher than the additional power consumption of the adsorption unit and its auxiliaries.
Doreen Acker, Software Developer at Fahrenheit GmbH, on the prototype optimization
In terms of the control software optimization, we are implementing two changes in the HyCool XHHP01 prototype. The first one is the introduction of a free cooling mode, to allow the use of low external temperatures for cooling of the compression unit’s condenser. In brief, in the free cooling mode the condensation heat of the compression chiller is dissipated directly to the ambient air via the dry cooler. If the outdoor temperatures are low enough to ensure the condensing temperature of the compression chiller as low as or lower than with the use of the adsorption chiller, which happens mostly in winter and during night time, the system will operate more efficiently in the free cooling mode. The operation of the system resembles the standard operation of the compression chiller and saves the electrical power needed to drive the circulating pumps of the adsorption chiller. Thanks to the clever hydraulic connections in the adsorption unit, we can implement this new operation mode through a software update without the need to rebuild anything in hydraulics. The second change is the optimized start-up procedure. After the tests performed by the colleagues from CNR, they suggested that the compression unit should be started when the temperature in the cold water circuit of the adsorption unit reaches a specified threshold. In this way, we will ensure favourable conditions for the operation of the compression unit at all times.
René Weinitschke, After Sales & Factory Service Engineer at Fahrenheit GmbH, on the data logging and Cloud solutions
In order to evaluate the performance of the hybrid heat pump, we have to perform measurements and collect meaningful data. Some of the measurements will be carried out by the main control system based on the sensors installed on the pipelines but there are also quite a few sensors installed inside the prototype. The values from these sensors will not be sent to the main control system; rather we plan to collect them in the Cloud. We have not used this technology so far, but its implementation in our commercial projects is one of our priorities. It will not only help our After Sales services, but also contribute to our technology development. HyCool is a great opportunity for us to test this solution! From the beginning, we have to place great emphasis on the data security, especially because the pilot plants will be installed in “real-life” factories.
According to the current execution plan, the optimized prototype of the hybrid heat pump is going to be delivered to the Bo de Debó demo site in October 2019. After proper installation and commissioning, the operation of the hybrid heat pump will be monitored for 12 consecutive months. Based on the collected data the Fahrenheit team will evaluate its performance. It is expected that due to the optimization measures implemented, the prototype will show even better performance than what was achieved during the first tests at CNR.