How to turn solar heat and industrial waste heat into useful cooling effect? Industrial processes are often energy-intensive and the need for their efficient decarbonization is now at the forefront of governmental and corporate policies worldwide. However, solutions for the green transition of the industrial sector should be:
- Flexible
- Widely applicable
- Reliable
And should:
- Minimize energy consumption
- Reduce operational costs
- Lower CO2 footprint
Is there a solution to all these answers? Heat pumps are the fit match to tackle these issues.
Within HYCOOL, CNR ITAE and Fahrenheit have developed a hybrid thermal heat pump for application in several industrial sectors where efficient and sustainable cooling is needed. But what is the hybrid heat pump?
The hybrid heat pump concept
HYCOOL system proposes the combination of a thermal heat pump with an electrical heat pump: the thermal heat pump exploits low-temperature waste heat (i.e. 70-90 °C) that is generally unused or dumped to the ambient. It can also be powered by renewable sources, such as solar heat and biomass. The electrical heat pump can exploit electricity locally produced (i.e. from PV panels or other sources) and thus further increase the share of renewables. The hybridization consists in the configuration of the two heat pumps: they can work in series, in parallel or in cascade by just changing the hydraulic connections. This makes HYCOOL configuration flexible and easily adaptable to different industrial cases.
In the framework of HYCOOL, two case studies are considered, which are shown in Figure 1:
- At GIVAUDAN (chemical industry), process cooling at +5°C is needed. To achieve this target with an overall high efficiency, the base load is covered with an adsorption unit (80 kW nominal power) that cools down the fluid in the range 5-21°C. Peak load is supplied by a compression unit with a natural refrigerant (propane, R290), that is connected in series with adsorption unit.
- At Bodedebò (food industry), cooling of food at -10°C is needed. In this case, the efficiency in cooling generation is achieved by using a cascade configuration: the thermal heat pump (adsorption) is used as topping stage for the electrical heat pump, in a two-stage system. This increases the efficiency of the electrical heat pump up to 40% at the expenses of renewable or even waste low-grade heat, so virtually without the need for extra cost.
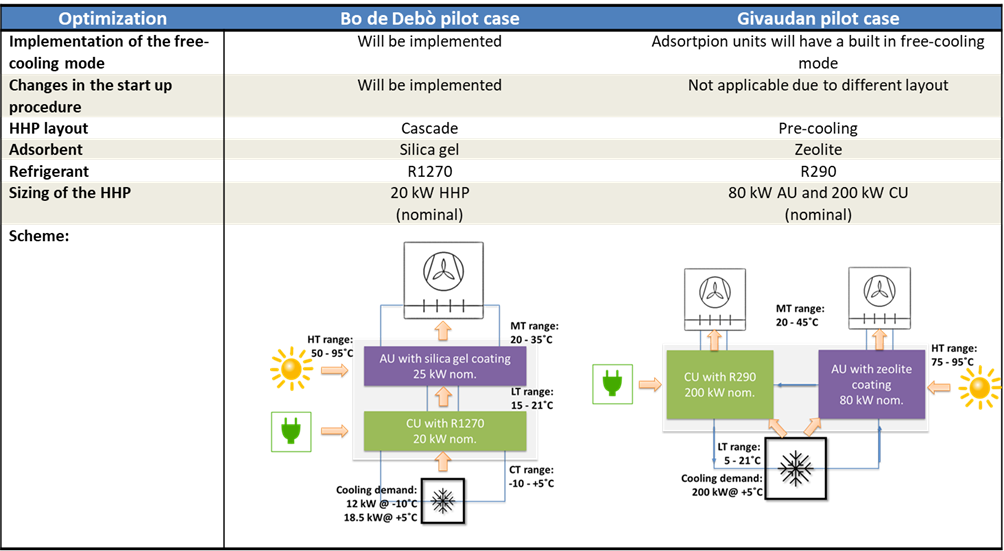
Experimental evaluation of the hybrid heat pump
The hybrid heat pump was tested in the laboratories of CNR ITAE in Messina in design and off-design conditions (see Figure 2). The aim of the tests was to define the cooling power and electricity consumption of the hybrid heat pump in the different ambient and process operating conditions, as well as confirm the reliability under off-design conditions. To this purpose, more than 100 testing cases were evaluated, and the results were reported in form of performance maps, like those in Figure 3.
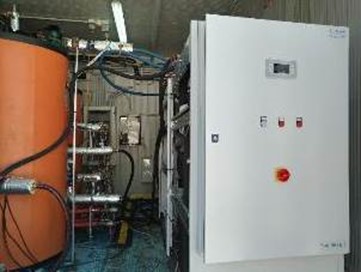
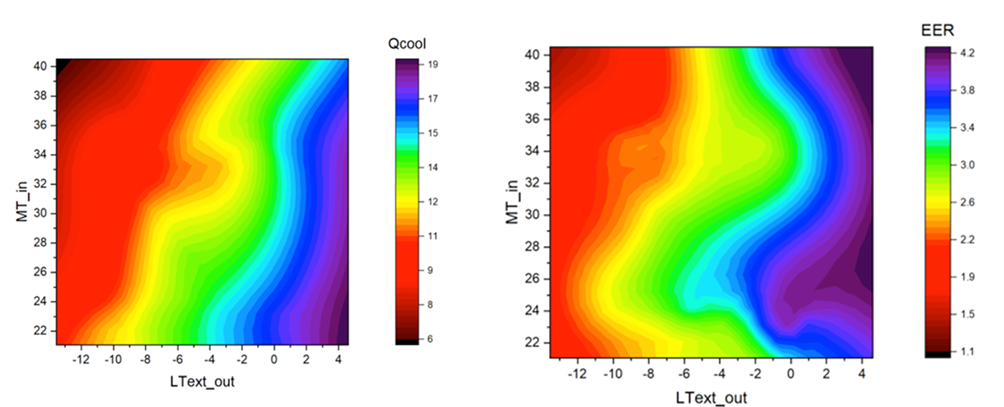
Is HYCOOL solution feasible for you?
HYCOOL solution is widely suitable for a vast range of processes. To know whether solar cooling can be part of your industrial processes, a screening tool, based on process requirements and information on the solar radiation in your industry’s location, was realized and is accessible here:
The results of the experimental testing at CNR, instead, were used to compile a calculator to predict the refrigeration capacity and energy efficiency ratio (EER) of the cascade HYCOOL chiller for a given industrial cooling process. You can access the tool here:
References
- Dino et al., Experimental characterization of an innovative hybrid thermal-electric chiller for industrial cooling and refrigeration application
Written by CNR-ITAE