After two years, and the COVID_19 lockdown consequences, the HyCool consortium has met again in person, to hold the 7th General Assembly in Barcelona. The event has been organized by the Project Coordinator Veolia and IDP Ingeniería during the 9th and 10th of November 2021. The objective of the Assembly has been to review and update the project progress and to discuss the final steps in a moment where the project is near to the commissioning stage.
The project has suffered several delays because of the COVID_19 crisis and for other consequences of it regarding the civil works execution, the limitations on the logistics and transport of the equipment from different points in Europe (Austria and Germany) to Spain where the pilots are being installed, and even, the availability of some of the core materials for the solar field installation. Nevertheless, the current situation is optimistic as almost 85% of the pilot works in Givaudan and Bo de Debó are completed including civil works, installation of equipment and the solar mirrors.
During the first session, work package leaders presented the progress made with the core technologies focused on the installation of the equipment, the demonstration activities, the exploitation, communication, and coordination activities.
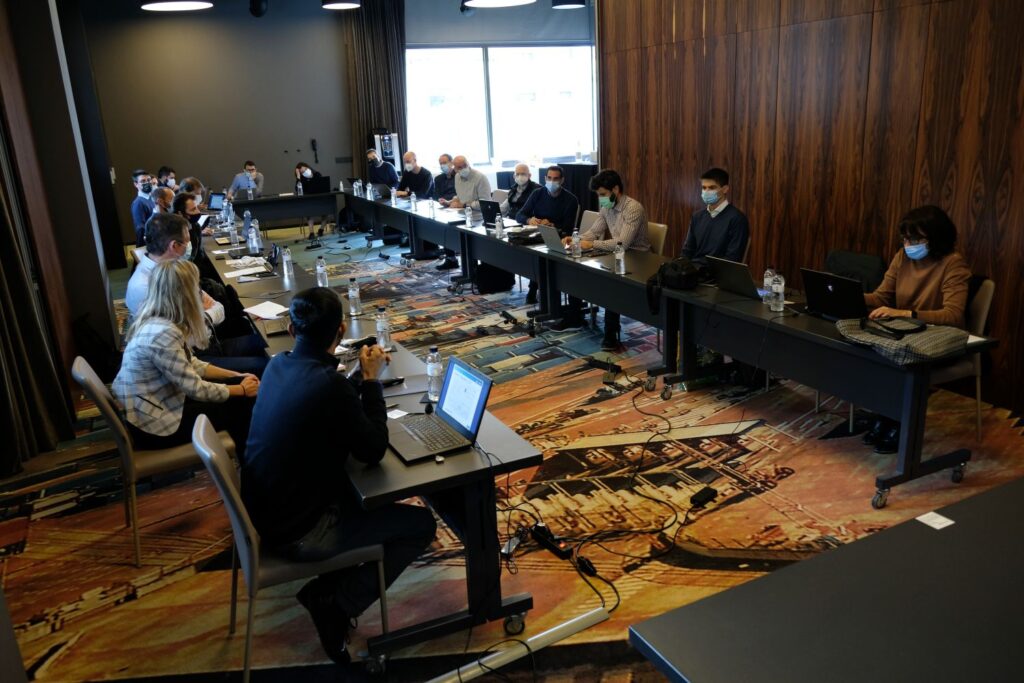
After the project coordinator Veolia welcome words, the partners involved in the manufacturing of the equipment, installation processes and the Pilot Site representatives discussed about the commissioning and demonstration stages next year when the project shall be closed. Up to now, the delays are minor and depend on some circumstances regarding adjustments and integration of the systems with the Energy Management system implemented by Ecotherm.
Many interesting results have been obtained and now work packages 7, 8 and 9 that cover environmental and socio-economic analysis, exploitation and communication activities may progress towards the planning of workshops, communication of energy management simulation tools available on the HyCool website, the potential commercialization of the technologies designed and implemented, and the visibility of the companies that have made conscious decision at introducing renewable energy in the industrial field. During the WP9 about communication and dissemination activities, COMET and the partners discussed about the coming events, workshops and training sessions based on Virtual Reality implemented by AIT, IDP and the support of Ecotherm and Fahrenheit.
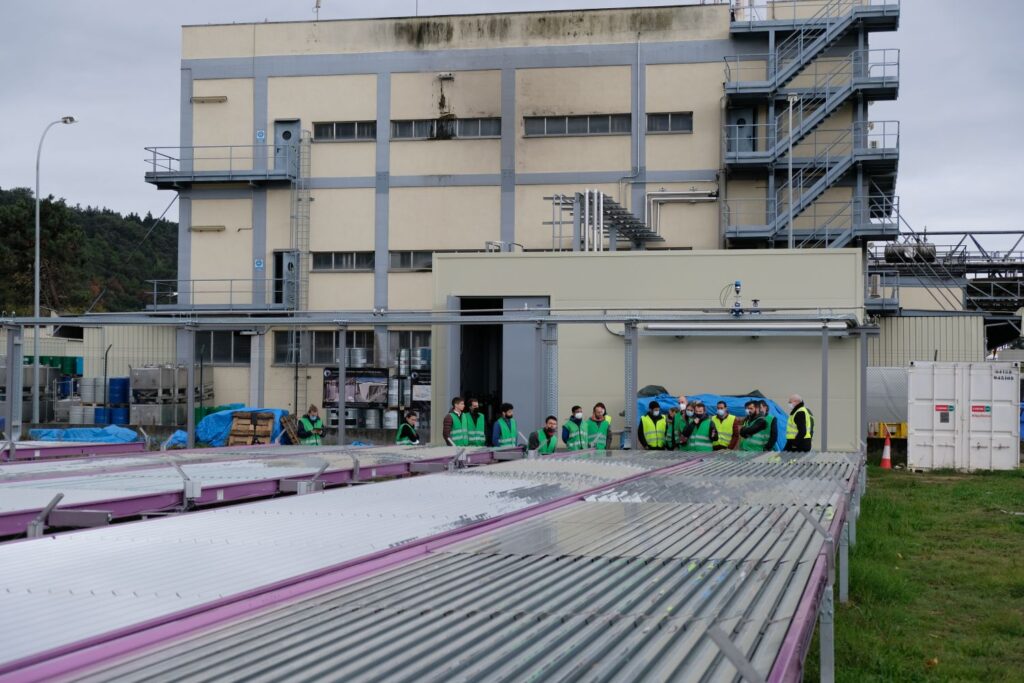
During the visits to the pilot sites, the partners could see the installations at Givaudan, the visit was focused on the solar field and the Ecotherm technical room. Ecotherm explained the process about the generation of steam and hot water from the solar energy collected in the solar panels, and the pending works until the commissioning.
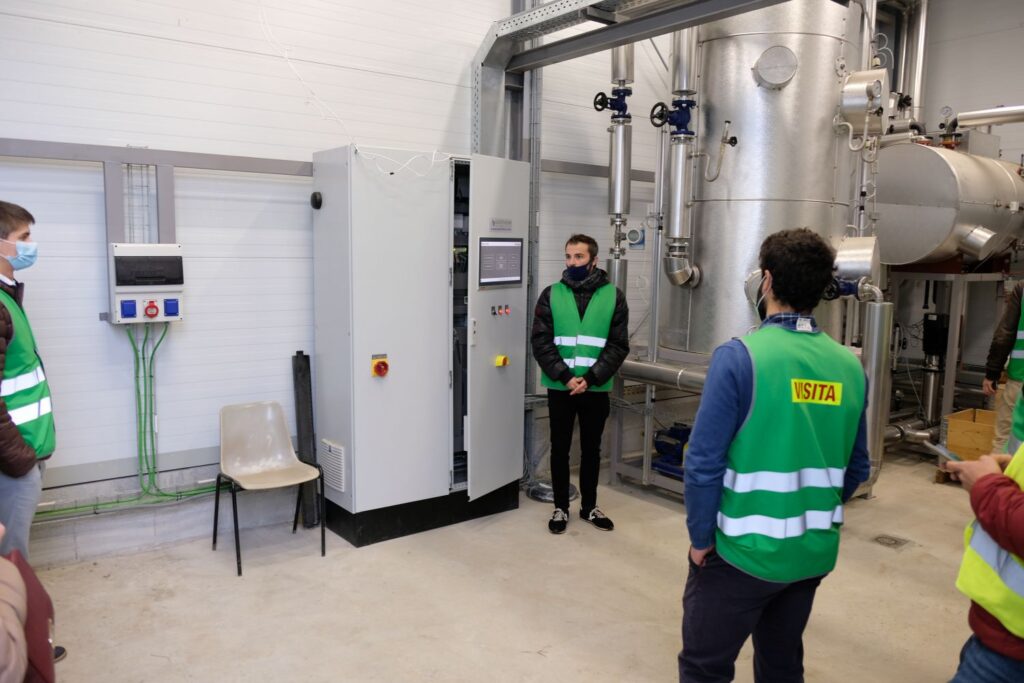
For the other hand, in Bo de Debò pilot site, the partners visited the technical room where Faherenheit and Ecotherm equipment are installed. The solar collectors are not yet installed because some structural works must be performed on the building that will support them.
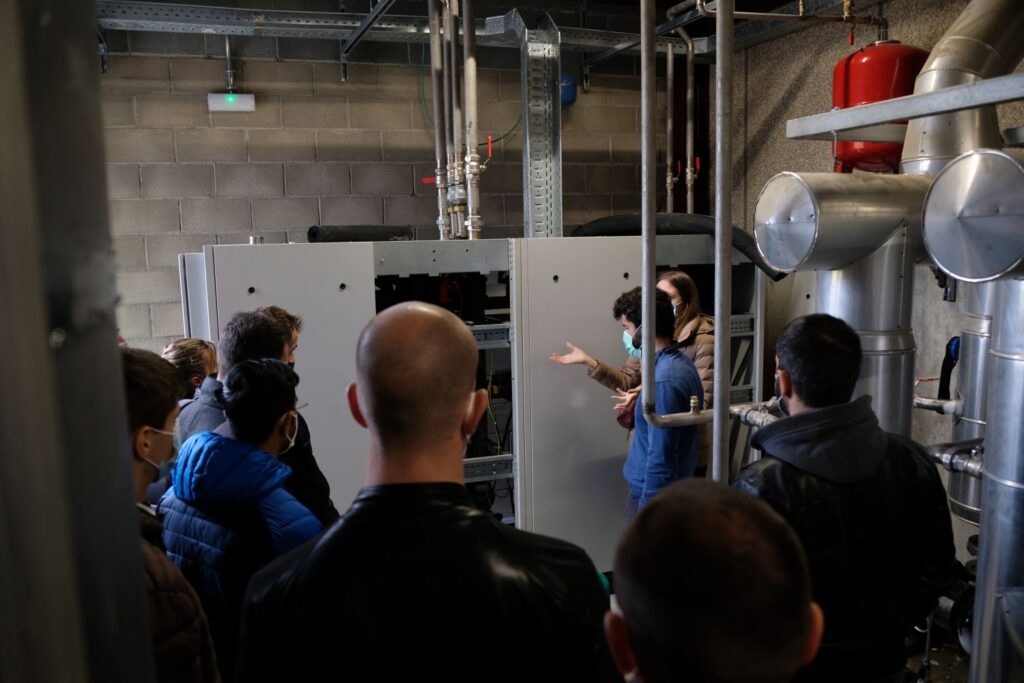
R2M also took advantage of this visit to scan the technical rooms and solar field with the Matterport camera to improve the virtual reality environment and some of the exploitation and commercialization activities planned. These results will be shared in further press releases and newsletters of the project.
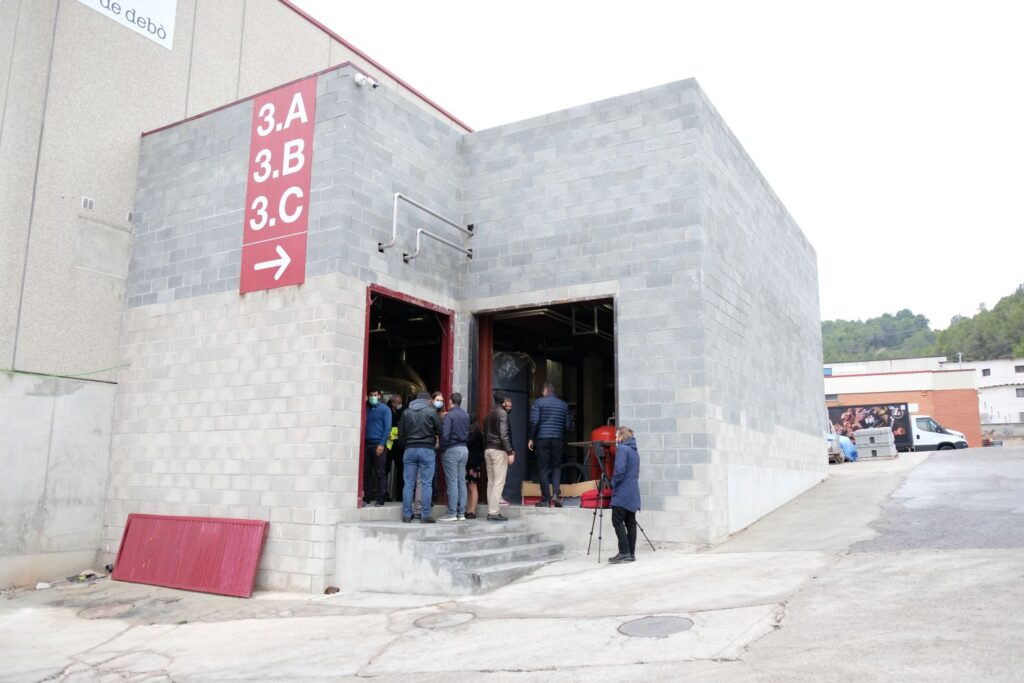
This is the first face-to-face meeting after COVID_19 crisis and with the works performed in a very finished stage. Next Assembly will be held in Germany around May 2022, but some visits and actions to the pilot sites shall happen in between.
HyCool Project is in its final stage and 2022 will make possible to demonstrate how efficient and profitable is the HyCool and thermo-solar energy in industry.