Within the HyCool project (Industrial Cooling through Hybrid system based on solar heat), a fundamental point is to determine the environmental and socio-economic benefits of the innovative HyCool solution compared to the state of the art.
The HyCool project will introduce for the first time the solar energy in industrial cooling systems, as the result of the integration of 3 main innovations (Figure 1):
- Solar steam generation (concentrating solar collectors);
- Phase change materials (PCM) storages; and
- Highly efficient and flexible hybrid chiller technology.
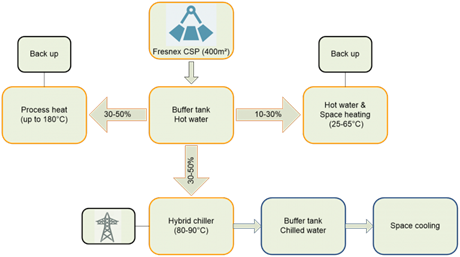
With the installation of the demonstration sites in Givaudan (chemical industry) and Bo de Debó (food industry), we are now getting to the heart of the demonstration activities, which will include the assessment of environmental and socio-economic impacts.
The HyCool System indeed will result in relevant benefits on the environment and the human health, as well as in important economic benefits thanks to energy consumption reduction (estimated in 75%) and operational GHG emissions reduction.
In particular, the assessment of environmental and socio-economic impacts aims to analyse, evaluate, understand and manage the environmental and health effects of the HyCool technologies and solutions, with particular reference to the Global Warming Potential (GWP), with the quantification of Greenhouse Gases (GHG) emissions considering the entire life up to the point of disposal.
The activities will be performed in the framework of Work Package 7, led by the partner CiaoTech srl (Italy), a consulting company specialised in innovation management.
Since the assessments are conducted with a comparative methodology, as a first step, we have identified and analysed the reference process, with most industrial cooling and refrigeration systems worldwide powered by electricity and employing big electrically driven vapor compression machines. Secondly, we have defined the main environmental parameters and indicators to be monitored during the assessments.
In the coming months, we will carefully and thoroughly analyse the HyCool technologies and system, first of all from the environmental point of view, taking into account all the phases of the life cycle as per ISO 14040 and ISO 14044 standards (Figure 2). This analysis is known as Life Cycle Assessment or LCA.
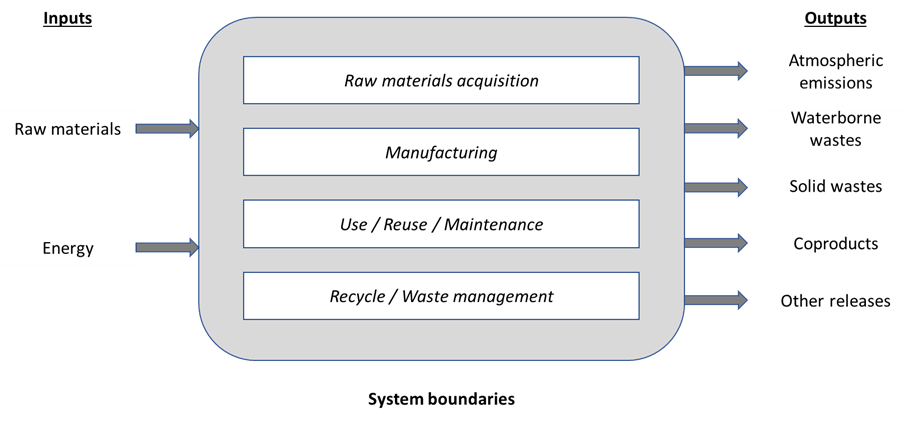
Thus, the LCA will allow us to quantify all inputs (resources and energy) and outputs (pollutants and wastes) of the solar cooling systems and assessing how these solar cooling systems affect the environment, by demonstrating the benefits of the HyCool System in comparison with the heating and cooling processes currently used in the industry.
We will then analyse the economic impacts of the developed innovative technologies by comparing them against the conventional practice with a view to demonstrate significant reduction in human labour intensity and cost, but also reduction in operating expenditures incurred by energy, water and material consumption.
Finally, the assessment will focus on the social impacts that the Hycool solutions will generate on society at large.
These activities will allow us to have a complete picture of the potential impacts deriving from the application of HyCool innovation in the world of industrial refrigeration and to demonstrate that solar heat can become a reliable energy source for greener, more energy-efficient industrial processes.
Written by Luigi Ranza, from CiaoTech